Decorative metal panel manufacturers are called upon, now more than ever before, to solve architectural solutions for exterior facades, screening, and overhead shade. These panels can be raw metals, made to rust, ornamental blacksmith work for artistic railings, or systems of panels designed to be installed easily and last as part of the architectural form.
But whether a product is decorative or structural, the designer, contractor, and customer all need to consider how building code affects the products they might want to use in the new space.
Interior screens may only need to meet deflection standards, meaning how much the panels move when you push on them. Guardrails and pool enclosures require a maximum hole size in the panels. Overhead shade needs to consider snow loads. And cladding on the outside of a building needs to be sure to stay attached in strong winds.
The engineering required for any project can be a serious matter, where cutting corners can cause permitting delays until structural calculations are reviewed. The question then becomes, “Who is the best qualified party to provide those structural calcs?” Most commercial projects have a project engineer, who can put together the documents required for a state-licensed professional engineer to stamp the drawings, in some cases, stamping it themselves. When reviewing all the products on a building, however, the question isn’t what each product is rated for, but rather, “What is the performance of the building, as a whole?” It’s the sum of the parts, and when a little artistic license of one thing adds to a little risk tolerance in another thing, the acceptable level of risk may outweigh the value of the aesthetics. But can’t any engineer just crunch the numbers to determine the qualifications of each decorative panel?
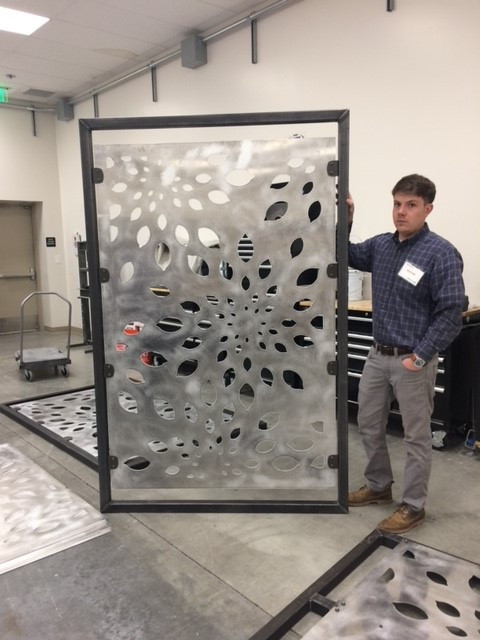
In today’s manufacturing landscape, it is easier than ever to fabricate custom things, and decorative metal panels are no exception. The more predictable a metal panel is, the easier it is to understand its structural integrity. Solid panels are easy to engineer if the material and finish are known. Industrial “perf” and expanded metals are likewise easy panel characteristics in running its geometry through structural analysis for different weather conditions and load scenarios.
But the more unpredictable the panel is, with artistic cutouts, bends, or inconsistent perforations, the more a typical engineer is going to require “over-engineering” to take out the risk of unknowns and to avoid delays in getting on to the next job.
Over-engineering means thicker panels, more structural support, more fasteners, and in the end, more dollars spent for the panel system and for installation. The way to reduce risk without increasing cost is to work with product manufacturers who have the experience (and software) to provide project guidance and structural calculations for each project, as needed.
Parasoleil has created a unique and decorative product with dependable lead-times, but their Design department staff also know that pretty things need to last, especially when it comes to architecture and public spaces. With the project guidance that they walk clients through, it’s only fitting that their next step was to offer a structural calculation report, specific to their project, patterns, and panel assembly.
In-house structural analysis is not required for every project. Often, relying on a product-manufacturer’s experience for what looks best is enough. But when value-engineering for a project’s risk and cost meet the uncertainty of building code requirements and getting a certificate of occupancy, there’s no better partner than one who proves the performance of their own product with numbers.
###
Parasoleil is a Colorado-based manufacturer of architectural panel systems to filter light and frame space. They are the 2017 recipients of the “Advancer of the Year” award from the Colorado Advanced Manufacturer Alliance.
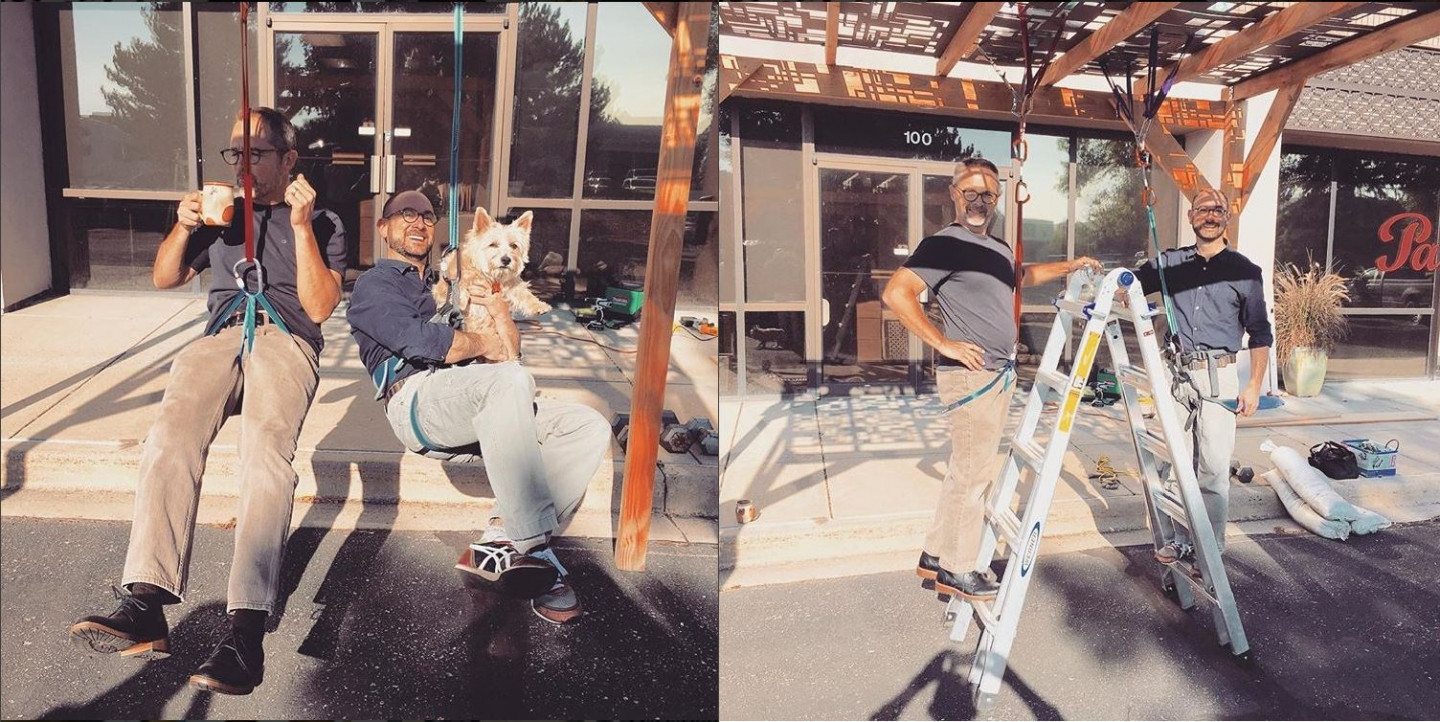